Understanding the Value of Timely Stretch Wrap Maker Repair Work Solutions
When it involves stretch cover equipments, timely repair services can make all the difference. You understand that also small mechanical or electrical issues can cause unforeseen downtime, affecting your manufacturing line. Resolving these troubles quickly not only protects effectiveness however additionally boosts the top quality of your wrapped products. So, what factors should you think about to ensure your equipments remain in leading shape? Allow's explore this crucial aspect better.
The Duty of Stretch Cover Machines in Modern Manufacturing
Stretch cover equipments play a vital role in modern-day manufacturing by guaranteeing that products are firmly packaged for transportation and storage. You count on these equipments to supply stability and protection, avoiding damage during transit. When you make use of stretch wrap, you lessen the threat of things moving or getting crushed, which can cause costly losses.
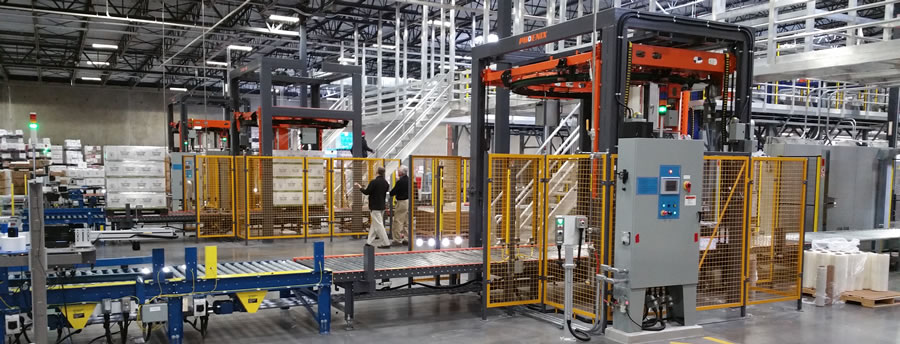
Moreover, making use of stretch wrap makers can improve your overall supply chain effectiveness. By improving the packaging procedure, you lower labor costs and speed up delivery times, making certain that your clients receive their items immediately. In today's hectic market, this benefit is crucial.
Common Problems That Lead to Equipment Downtime
When your stretch cover device experiences downtime, it can frequently be traced back to mechanical failures or operator errors. Comprehending these common problems can aid you stop expensive disruptions. By dealing with these factors, you can maintain your operations running smoothly.
Mechanical Failings and Break Downs
When parts put on down or break, your stretch cover machine may stop suddenly, impacting efficiency. Furthermore, electric failures can create breakdowns in the device's control system, creating additional hold-ups. By focusing on prompt repair services, you're not only decreasing downtime however also expanding the life expectancy of your equipment.
Driver Mistakes and Oversights
While operators play a vital duty in the smooth functioning of your stretch cover device, their errors and oversights can cause substantial downtime. Usual concerns like inappropriate loading, incorrect setups, and failing to keep an eye on wrap tension can cause delays and item damage. For example, if an operator disregards to look for worn-out movie, it can cause irregular covering and enhanced waste. Furthermore, miscommunication during shifts can cause crucial adjustments being overlooked. It's vital to give thorough training and normal refresher courses to reduce these mistakes. Encouraging a society of accountability and watchfulness amongst your team can substantially decrease downtime. Eventually, spending in driver training pays off by enhancing performance and extending your machine's life expectancy.
The Financial Impact of Postponed Repair Work
Postponing repair services on your stretch cover maker can cause significant financial repercussions that surge with your entire procedure. When your device breaks down, efficiency plummets. Each hour of downtime can cost your business not just in lost outcome, however also in labor expenditures as employees stand idle. You may additionally face boosted product wastage as a result of incorrect wrapping, causing greater costs for packaging products.
Furthermore, prolonged hold-ups can escalate small concerns into significant issues, needing a lot more considerable repair services or perhaps full replacement of the maker. This can strain your budget plan and interfere with cash money circulation. Hold-ups can likewise affect your distribution routines, hurting client fulfillment and potentially triggering you to shed service to competitors. Ultimately, prompt repair services are necessary to keeping your profits and guaranteeing smooth procedures. Don't ignore the financial effect of overlooking those fixing needs.
Advantages of Proactive Upkeep Programs
Prompt repair work can conserve you from pricey downtime, but executing a proactive maintenance program takes it a step better. This not only keeps your stretch wrap machine running efficiently however additionally expands its lifespan.
With less interruptions, your workforce can concentrate on their tasks without the stress and anxiety of sudden machine failures. Keeping peak performance can boost the quality of your wrapped products, guaranteeing client satisfaction.
Identifying Signs That Your Equipment Requirements Repair
As you operate your stretch wrap equipment, it is essential to stay attentive for indicators that indicate it might require repair work. One of the first points to seek is uncommon sound. If you hear grinding, squealing, or any type of other odd noises, it can indicate a hidden concern. Additionally, look for inconsistent wrapping. If the movie isn't stuck properly or you notice go to website uneven stress, your equipment could be malfunctioning.
Another indication is a boost in downtime. If your device often stops or requires modifications, it is time to check out. Maintain an eye on the equipment's rate; if it's slower than typical, something could be wrong. Any type of noticeable damages like frayed cable televisions or leakages ought to not be disregarded. Promptly addressing these indications can avoid extra significant troubles down the line, ensuring your procedures run efficiently.
Choosing the Right Repair Service for Your Demands
Exactly how do you select the best repair service for your stretch cover machine? Consider their experience and experience. Seek specialists who concentrate on stretch wrap machines and have a tried and tested track document. Check on-line reviews and reviews to determine consumer complete satisfaction.
Next, examine their reaction time. A trusted service should provide prompt support, as device downtime can be costly. It's additionally vital to recognize if they give emergency situation repair services.
Don't neglect to ask regarding warranties on repair work and components. A trusted solution supports their work, giving you satisfaction.
Last but not least, contrast pricing but avoid picking entirely based on price. Occasionally, the least expensive choice may bring about substandard service. By considering these variables, you'll find a repair service that satisfies your needs and keeps your stretch wrap maker running efficiently.
Approaches for Lessening Stretch Wrap Equipment Downtime
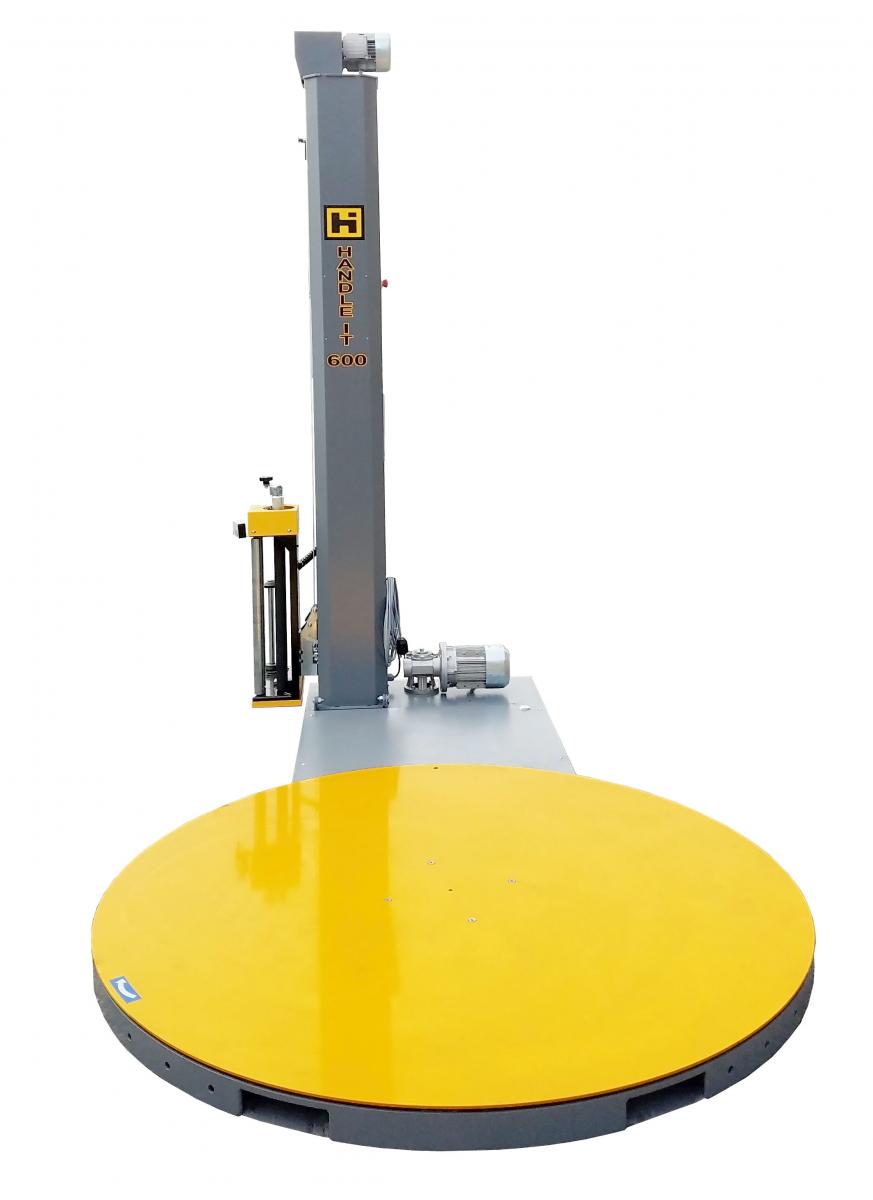
Training your operators is another crucial method. Furnish them with the expertise to determine and address small problems before they result in significant breakdowns. Motivate them to maintain a log of any abnormalities, which helps in diagnosing concerns faster.
In addition, keeping an inventory of essential extra parts can drastically minimize downtime. When something breaks, having the best components accessible means you will not have to wait for deliveries.
Finally, think about purchasing real-time monitoring systems. These systems can alert why not try these out you to efficiency modifications, permitting instant treatment. By applying these techniques, you'll keep your stretch cover machine running efficiently and effectively.
Frequently Asked Questions
Just How Usually Should Stretch Wrap Machines Be Serviced?
You must service stretch wrap machines regularly, ideally every six months. However, if you notice any type of performance issues or unusual sounds, don't wait-- schedule upkeep immediately to stop costly break downs and guarantee peak effectiveness.
What Are the Regular Prices Related To Stretch Wrap Device Fixes?
Regular expenses for stretch wrap equipment repair services vary, yet you might expect to invest between $200 to $1,500 depending upon the concern. Regular maintenance can help lessen these prices and expand your maker's lifespan.
Can I Perform Fundamental Maintenance on My Stretch Cover Equipment?
Yes, you can do basic maintenance on your stretch wrap maker. Frequently look for wear and tear, cleanse the components, and warranty appropriate lubrication. Maintaining it healthy can expand its life-span and enhance performance.
Just how Do I Know if a Fixing Solution Is Trusted?
To locate a trustworthy fixing service, inspect online evaluations, ask for recommendations, and validate certifications. A dependable service will offer clear estimates, service warranty options, and prompt interaction, ensuring you really feel certain in their proficiency.
What Should I Do in Situation of an Emergency Situation Machine Breakdown?
In instance of an emergency device breakdown, you ought to right away quit procedures, analyze the issue, and contact your repair solution. Keep crucial get in touch with numbers convenient, and record the problem for effective check my source repairing when assistance gets here.
Verdict
To summarize, understanding the importance of prompt stretch wrap device repair work can considerably enhance your operations. Keep in mind to stay vigilant for indications of wear and choose a trusted repair service to maintain your devices running smoothly.